How Manufacturers Are Navigating Ongoing Supply Chain Issues Post-COVID
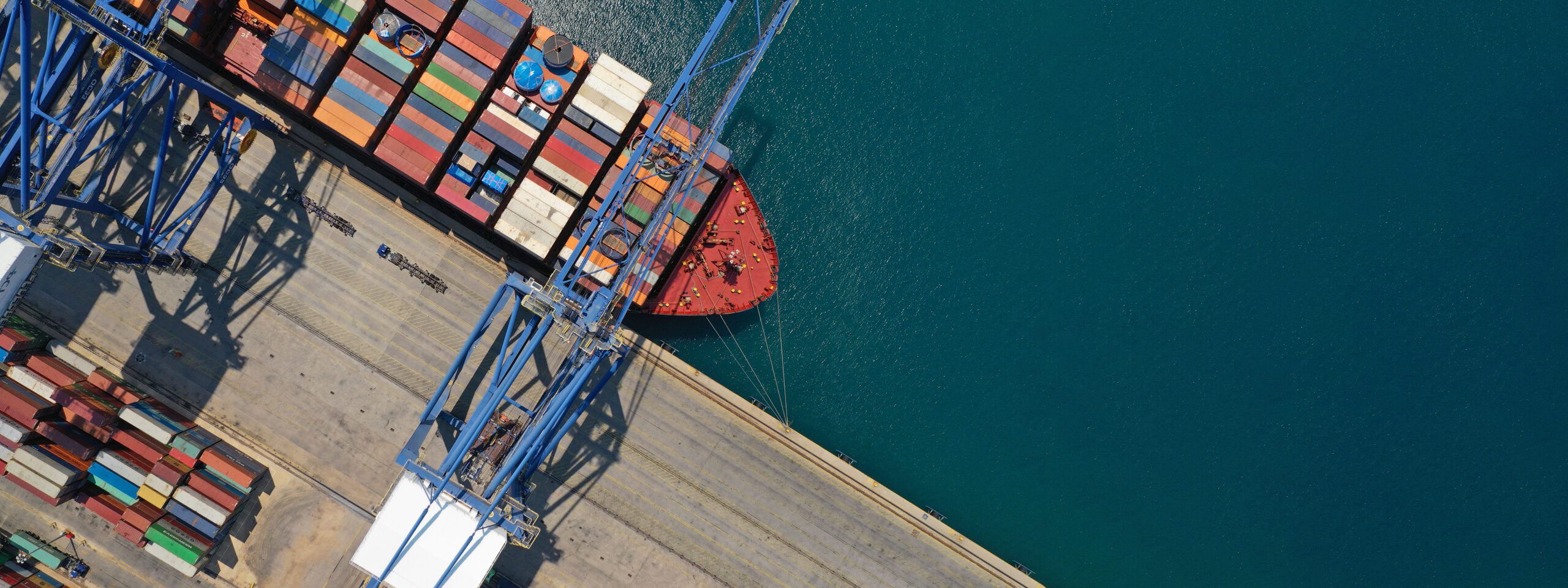
Four years after COVID-19 upended global supply chains, manufacturers are still feeling the ripples of disruption within their businesses.
Despite progress in supply chain efficiency, the industry continues to encounter significant hurdles in procuring essential materials, which are impacting both costs and production schedules.
For instance, during the pandemic, food manufacturers faced significant difficulties sourcing jar lids. Though these items are now available, lead times remain extended and prices have surged for some of our CJBS clients.
Here, we’ll dive a little deeper about how those supply chain issues are still permeating today, how they’re impacting financials, as well as provide some strategies for managing these supply chain complications.
Today’s Supply Chain Landscape
The pandemic introduced seismic shifts in global supply chains, creating a cascade of challenges that companies are still working through to this day.
Factory closures, lockdowns, and decreased production capacities triggered widespread delays and shortages throughout the manufacturing space.
Today, labor shortages persist as industries struggle to rebuild their workforce. Shipping delays, exacerbated by geopolitical tensions and sustained consumer demand, further complicate matters and make production planning difficult. The boom in e-commerce has led to a sustained high demand for packaging materials, keeping supply tight and prices elevated.
Material shortages remain a persistent challenge. The pandemic’s surge in online shopping has left an enduring demand for packaging components. As a result, manufacturers face higher costs and prolonged lead times, reflecting the ongoing imbalance between supply and demand, the global cardboard shortage of 2023 being one example.
Transportation bottlenecks also persist. Port congestion and shipping delays have led to a significant increase in freight costs, placing additional financial strain on manufacturers. These logistical hurdles exacerbate production delays and elevate overall expenses.
Supply Chain Financial Implications for Manufacturers
Increased Costs – The scarcity of materials has driven up prices, exerting pressure on profit margins. In particular, the cost of packaging components has significantly increased, which mirrors the broader trend of rising expenses across the supply chain.
Cash Flow Concerns – Supply chain disruptions have a notable effect on cash flow and financial planning. Delays in production schedules can push back revenue realization and create cash flow challenges. For example, if a manufacturer experiences a month-long delay in receiving critical components, this can extend the time between production and sales, complicating cash flow management.
“Our goal is to work diligently with our clients to determine the most economical way to utilize your capital,” says Lorena Engelman, CPA & senior member of CJBS.” Whether it’s purchasing supplies with potentially long lead times, or considering machinery with high interest rates, you need to make the most effective use of your capital at the time. We provide the high level analysis that is essential to making informed decisions for your business.”
Shifting Demand and Forecasting Challenges – Shifting demand patterns further complicate forecasting efforts. The pandemic has altered consumer behaviors and led to unpredictable swings in demand. Manufacturers must adapt to these shifting demands by refining their forecasting models to better anticipate and respond to market fluctuations.
Changing Budgets – In response to rising costs and shifting demand, manufacturers are revising their budgets and pricing strategies. This might involve increasing the price of finished goods to offset higher material and production costs or implementing cost control measures to mitigate expenses. According to Supply Chain Management Review, 55% of organizations planned to increase their supply chain budgets in 2024.
Strategies for Managing Supply Chain Challenges + Tech & Innovation
Diversification of Suppliers
One effective strategy for managing supply chain issues is diversifying suppliers. By avoiding dependence on a single source, manufacturers can reduce risk and enhance supply chain resilience. Exploring multiple suppliers across different regions can help ensure continuity and mitigate the impact of disruptions.
Inventory Management
Improving inventory management is essential for navigating shortages. Techniques such as maintaining safety stock levels and utilizing advanced forecasting tools can help manufacturers better control their inventory and reduce the impact of supply chain issues. Embracing technology for real-time tracking and analytics can further enhance inventory control.
Digital Solutions
Technology offers transformative solutions for managing supply chains. Advanced software systems provide real-time insights into inventory, supplier performance, and production schedules, while AI algorithms enhance forecasting accuracy and optimize processes. Real-time tracking and data analytics tools help predict potential disruptions and recommend corrective actions to streamline operations. AI also supports predictive maintenance and automated procurement to reduce downtime and streamline supplier management.
Innovative Practices
Adopting innovative practices can also help manufacturers tackle supply chain challenges. Investments in automation and advanced manufacturing technologies can improve efficiency and reduce reliance on manual processes. Additionally, incorporating sustainable practices, such as using recycled materials, can enhance supply chain resilience and address long-term risks.
Financial Planning
At CJBS, we offer support to manufacturers by crafting detailed financial plans that address potential risks. Here’s how we help:
- Cash Flow Forecasting: We help you forecast for possible disruptions, like delays in getting materials or sudden changes in demand. This way, you can plan for cash flow issues and stay on track even when things don’t go as planned.
- Budget Adjustments: We assist in updating budgets to reflect rising material costs and shifting demand. This might mean adjusting product prices or finding ways to cut costs.
- Risk Management: We also offer advice on managing financial risks, such as using hedging to handle price fluctuations or exploring different financing options to maintain liquidity.
The future of supply chains will likely involve continued evolution as industries adapt to new realities. Manufacturers who remain agile and prepared will be better positioned to handle future disruptions and seize emerging opportunities.
Manufacturers facing supply chain hurdles should seek professional guidance to develop effective strategies for managing these issues. At CJBS, we pride ourselves on being CPAs Who Care. We stick with our clients for the long term and are here to help you navigate the complexities of supply chain disruptions and maintain financial stability.